The machine is super! With it, the National University of Lesotho (NUL) effortlessly produces Mohalalitoe bar soaps, as the machine takes part in giving the bars a professional shape. It is based on the principle of “leverage” in physics where you do more stuff with less effort.
business
July 11, 2019
4 min read
Fokothi graduate makes soap machine
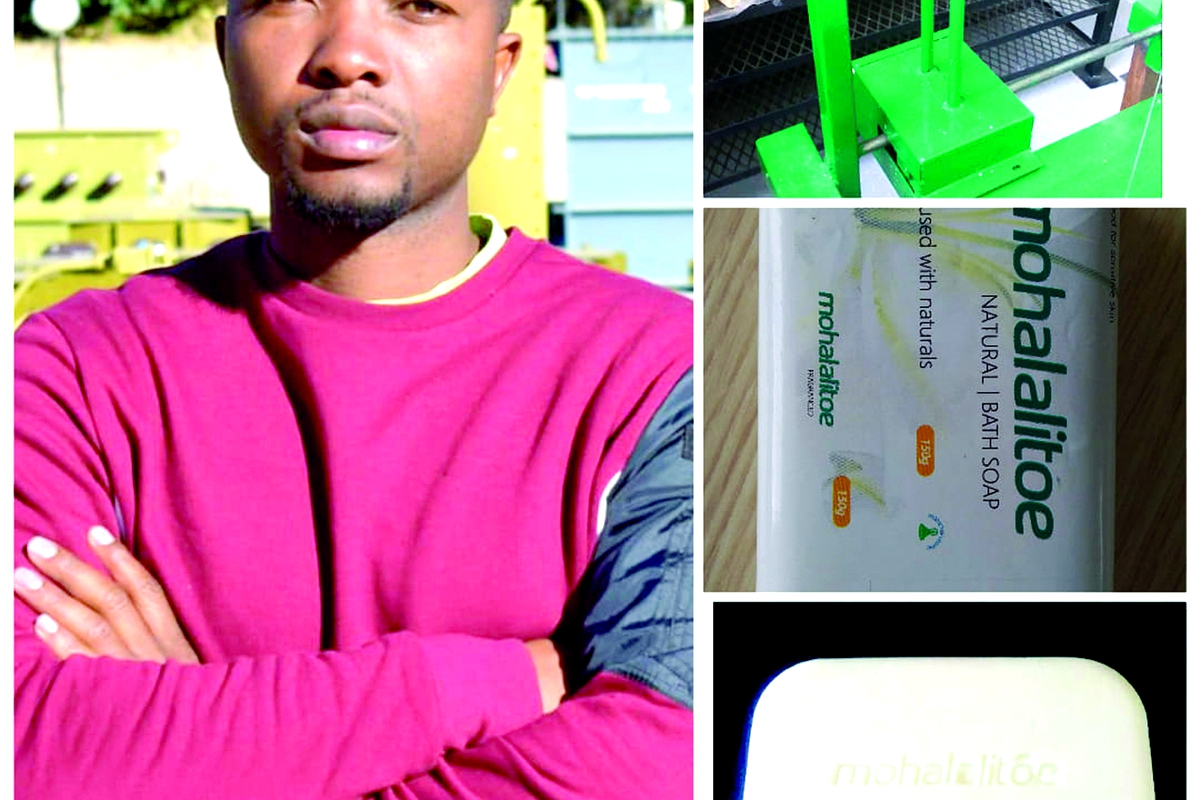
Mohalalitoe
“With this machine, Mohalalitoe soap producers get the work done in a matter of seconds per cycle, using just their hands. Plus it can be used by just about anyone,” said the obviously elated Ts’epo Lekola, the Lerotholi Polytechnic (Fokothi) trained machinist. The result is a soap that rivals regional soaps in form and quality. Mr Lekola credits Fokothi veteran instructors such as Potlako Rakotje, Thabo Mosoang and the ever enthusiastic Joseph Thaba as some of the people who instilled the love for hard work and entrepreneurship in him. “In fact I once worked with this team in a project in which Fokothi collaborated with the NUL to produce a waste processing machine - I was still a student then,” Mr Lekola said.
You may or may not be aware of it but NUL and Fokothi were made for each other. They just haven’t exploited the potential of collaboration enough. One was born in 1905 and emphasises practice (Yes! Fokothi was actually conceptualised in 1894 by Chief Lerotholi!). Another was born in 1945 and emphasises theory (NUL). Bring the two together and you brew an exceptional recipe! Plus the two national institutions are also known to punch above their weights when all odds are stacked against them. Take this Mohalalitoe project as an example.
Enjoy our daily newsletter from today
Access exclusive newsletters, along with previews of new media releases.
In case you didn’t know, Mohalalitoe is that natural soap developed by the NUL Innovation Hub. It has just been proved to be more superior to five other South African-manufactured soaps in most desirable properties. And Basotho really, really love it! However, as those with an inch of experience in manufacturing design will tell you, making a product and creating a process to make that product, are two different things. In fact, creating a process to make a product is the hardest part of manufacturing. Yet it is manufacturing, more than anything else, that forms the bedrock of any thriving economy.
No wonder the NUL Innovation Hub puts manufacturing at the forefront of its efforts. But here was a problem. Although the highly educated Chemical Technologists at the Hub created Mohalalitoe and perfected it within four years, when it came to producing the soap on a large scale, the tables were turned against them. So they had two options. They could either buy readymade soap-making machines from overseas. Or they could tap into the local talent to produce the machines.
Three things informed their decisions. One, they wanted to set up a processing plant with the lowest cost possible. Two, they wanted to have machines that would be durable but easy to repair. Three, they wanted a fast machine that would need little to no effort to use, and that would be manual to create jobs. Such a machine could only be made locally. “Local is lekker.”
For the two main machines now used to make Mohalalitoe, one was made by Mr Lekola’s company (Plug Holdings) in Lesotho, and another was made by two different companies in South Africa (NUL Innovation Hub is working a lot with our beloved neighbours these days). In case you didn't know, South Africa is very “local.” So the Mohalalitoe folks consulted Mr Lekola with strict instructions, “assist us to make a machine that would meet those three requirements.”
They made it clear that the machine was expected to work in unison with the ones made in South Africa, to deliver soaps with a near-perfect shape, cut and finish. “I was not overwhelmed with the requirement,” Lekola said. “However, I had never made a machine of that sort before, so I had to make my own research.” He did not like what he found. “The designs of the machines I saw were cumbersome and the machines were heavy when operated,” he said. “So I learned from their mistakes and I was determined to design a machine that would have all the requirements of the client.”
Drawing from a rigorous training obtained from years spent at Fokothi and his experience working for Phillips Lighting, he was more than the right man for the job. “When I worked at Phillips Lighting, we used to assemble a machine of more than 50 parts - I learned a lot about machine design in the process,” he said. “The result is a machine that works flawlessly to produce the ever popular Mohalalitoe,” boasted one of the machine owners. As a bonus, the machine was made in Lesotho. Therefore it will be repaired in Lesotho when it needs maintenance. Isn’t that great?
(Catch him here : 58404506, 62000413, plugonholdings@gmail.com, Facebook: @plugonholdings)